Un estrusore bi-vite viene normalmente utilizzato per ottenere dei materiali compositi formati da un polimero base al quale vanno aggiunti vari tipi di componenti per modificarne le caratteristiche (tipo colore, durata, lavorabilità ed altre caratteristiche) e renderlo quindi adatto ad una specifica applicazione.
In funzione quindi del risultato finale che ci si propone di raggiungere esistono vari modi per alimentare l’estrusore e che di seguito elenchiamo pur non avendo la pretesa di coprire tutte le possibili combinazioni.
Alimentazione dalla bocca principale dell’estrusore con un lotto (batch) pre-mescolato
L’alimentazione di un estrusore bivite viene spesso eseguita attraverso la tramoggia principale che viene fornita come standard in tutti gli estrusori Labtech.

Molti produttori di masterbatch utilizzano resine in forma di polvere premescolate con pigmenti, fillers e con cere polimeriche. In questo caso il pre-mescolamento viene ottenuto utilizzando mescolatori ad alta velocità (tipo Labtech LMX25-VS e LMX75-VS), nei quali il batch, durante il mescolamento, può raggiungere temperature di 80°C causando la fusione delle cere che vanno così a rivestire le resine ed i pigmenti. In particolare questo metodo viene utilizzato quando si possono usare le resine in forma di polvere.
In questo caso il pre-mescolamento serve per garantire anche una buona pre-dispersione poiché il pigmento in qualche modo viene già rivestito dalla cera e spesso da luogo ad una più alta ed uniforme concentrazione del pigmento nel masterbatch.
Tuttavia molte resine sono disponibili solo in granuli e non in polvere e sappiamo che non è possibile mescolare granuli con alte concentrazioni di pigmenti o altre polveri perché la miscelazione non risulterà omogenea e tenderà a separarsi. Normalmente i granuli si mescolano con piccole percentuali di polveri, che così rimarranno separate in fondo al contenitore e la miscelazione non sarà omogenea, causando importanti variazioni di concentrazione nel prodotto finale. Inoltre se la resina e le polveri non sono mescolate omogeneamente, si rischia di avere sezioni del bi-vite che lavorano solo sui pigmenti o su altre polveri senza che vi sia resina nei paraggi e ciò causerà pessima dispersione, possibile agglomerizzazione delle polveri o dei pigmenti oltre che un considerevole attrito sulle viti e sulla camera di estrusione.
Alimentazione dalla bocca principale utilizzando 2 o più tramogge

Se il batch che si vuole ottenere non è facilmente mescolabile come visto in precedenza, un’opzione è quella di utilizzare più tramogge all’ingresso della camera di estrusione che convergano sulla bocca di alimentazione principale. In questo caso, per esempio si può destinare una tramoggia all’alimentazione della polvere ed una seconda tramoggia per l’alimentazione del granulo. La polvere può essere a singolo componente oppure una mistura di varie polveri differenti. La tramoggia di alimentazione dei granuli deve essere mono-coclea mentre quella per alimentazione delle polveri deve essere a doppia coclea. Naturalmente l’utilizzo della tramoggia volumetrica rappresenta la soluzione più economica.
Tuttavia non è facile raggiungere la precisione di miscelatura richiesta che prevederebbe una calibrazione lunga e complessa ma in definitiva non molto affidabile. Questo è il motivo per cui si consiglia l’utilizzo di alimentatori gravimetrici di grande precisione in qualsiasi situazione di lavoro. Tuttavia, anche in questo caso ci sono delle limitazioni circa la quantità di materiale che si vuole alimentare. In questo caso la resina e la polvere vengono alimentate separatamente ed i granuli che entrano in camera di estrusione inizieranno la loro fusione solo dopo aver percorso un tratto a contatto con le viti, potrebbe essere solo quando raggiungono la sezione con gli inserti di mescola o ancor peggio solo quando arrivati all’interno della sezione di mescola. Va anche considerato che la polvere in qualche modo agisce come un isolante e quindi rallenterà il processo di fusione dovuto al calore proveniente dalla camera. Si può quindi generare un consistente attrito che nel tempo danneggia sia le viti che la camera di estrusione. Di conseguenza la dispersione della polvere nel prodotto finale può peggiorare. Questo pone un limite all’alimentazione di granulo e polvere dalla stessa sezione di entrata nella camera di estrusione. Tuttavia si può migliorare la situazione aggiungendo un agente disperdente nella polvere, per esempio una cera polimerica.
Lo scopo di utilizzare uno o più alimentatori laterali
La funzionalità dell’utilizzo di un alimentatore laterale è quella di introdurre materiale aggiuntivo nell’estrusore bi-vite. Esso viene usato per esempio quando non è possibile alimentare materiali in forma diversa (granuli, polveri, additivi ecc.) dalla tramoggia principale, come già spiegato precedentemente. Generalmente un alimentatore laterale viene posizionato dopo il primo set di dischi mescolatori (kneading discs, vedere figura sotto).

La camera di estrusione avrà un’apertura in corrispondenza del punto di entrata nel quale l’alimentatore verrà flangiato, con le viti che entrano leggermente nella camera di estrusione.
Le viti dell’estrusore (che sono componibili) in corrispondenza alla sezione di entrata dell’alimentatore laterale sono fatte in modo che non vi sia rapporto di compressione in modo da poter ricevere il materiale che viene introdotto attraverso l’alimentatore laterale.
La resina che viene alimentata attraverso la bocca di alimentazione principale sarà completamente fusa ed omogeneizzata in corrispondenza dell’alimentatore laterale. In questo punto le viti dell’estrusore devono essere profonde e con un passo appropriato in modo da accogliere tutto il materiale proveniente dall’alimentatore laterale. Bisogna inoltre assicurarsi che il materiale proveniente dall’alimentatore laterale sia alimentato in modalità “starve” (affamata), in modo che non si creino ingorghi.
A questo punto bisogna coordinare le velocità di alimentazione delle viti dell’estrusore e dell’alimentatore laterale in modo da poter realizzare la concentrazione desiderata.
Uso di tramogge volumetriche per alimentatori principale e laterale
L’alimentatore laterale da solo non può essere utilizzato come dosatore. Esso alimenta solamente, agisce cioè come un propulsore che invia materiale nella camera di estrusione. Quindi, per poter funzionare correttamente, ha bisogno di un’unità di dosaggio a monte in modo da poter ricevere il rate di alimentazione predeterminato.
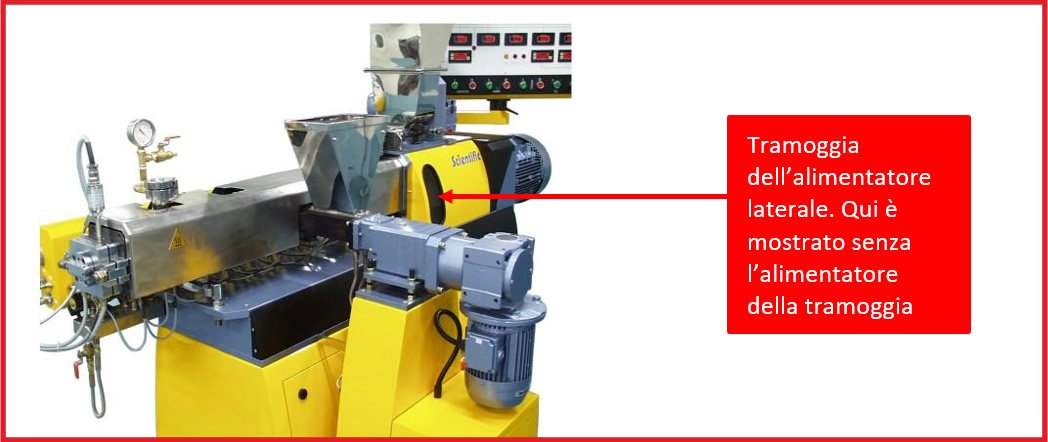


Naturalmente la soluzione meno costosa sarebbe quella di avere una tramoggia volumetrica a monte dell’alimentatore laterale, ma questa soluzione non è di così facile utilizzo. Se l’estrusore non è provvisto di alimentatore gravimetrico esso avrà la tramoggia volumetrica standard che alimenta la bocca principale dell’estrusore. Tuttavia, se la configurazione dell’estrusore prevede l’utilizzo di alimentatori gravimetrici, questi dovranno essere alimentati da tramogge volumetriche.

Questa dovrebbe essere la configurazione degli estrusori bivite quando utilizzati per lavorare polveri ma non granuli. Se si utilizza la tramoggia volumetrica sull’alimentatore laterale, questo dovrà esser calibrato insieme alla tramoggia volumetrica sull’estrusore. La calibrazione deve essere fatta lasciando girare gli alimentatori ad una certa velocità rotazionale (in RPM) e quindi misurando quanto materiale esce dall’alimentatore (in grammi o altre unità di misura).
Quindi, per esempio, se si fa girare l’alimentatore principale a 100 rpm, bisogna poi misurare quanti granuli escono dall’alimentatore a tale velocità. Supponiamo che escano 400g al minuto che vuol dire 24kg/h. Ora sappiamo che l’alimentatore principale rilascia 24 kg/h di granuli di plastica.
Ora supponiamo che, per esempio, si abbia una formula dove si richiede che il composto contenga il 20% di polvere che deve essere alimentata attraverso l’alimentatore laterale nella camera di estrusione dell’estrusore.
Quindi bisognerà produrre un totale di 30 kg/h di cui 24 kg/h saranno forniti dall’estrusore e 6kg/h di polvere. Quindi bisognerà regolare la velocita delle viti dell’alimentatore laterale in modo che rilasci 6kg/h. Per esempio questo potrebbe avvenire ad una velocità rotazionale di 50 RPM.
Ora siamo pronti a lavorare con l’estrusore bi-vite per produrre 30 kg/h di questo masterbatch, quindi si deve, come sempre con gli estrusori bi-vite avviare l’impianto a basso numero di giri, per esempio a 20 RPM, per produrre una piccola quantità di granuli di plastica. Il bi-vite deve sempre essere alimentato in modalità “starve”, che vuol dire che le viti vanno alimentate con una quantità inferiore a quella che esso può gestire. Si procede quindi a piccoli incrementi della velocità di rotazione del bivite e di conseguenza si incrementa un po’ la quantità di granuli, sempre facendo attenzione a stare al di sotto della capacità totale del bi-vite fino a quando si raggiunge la situazione dove l’alimentatore principale è a 100 RPM (a questo punto le viti dell’estrusore potrebbero girare a circa 400 RPM).
Ora si lavorerà sull’alimentatore laterale della tramoggia sovrastante. L’alimentatore laterale può lavorare ad alta velocità, mettiamo a 500 RPM, per essere sicuri che possa spingere tutta la polvere che si trova nella tramoggia volumetrica superiore dentro l’alimentatore laterale, che può essere avviato direttamente a 50 RPM per la calibrazione effettuata in modo da rilasciare 6 Kg/h.
A questo punto si stanno rilasciando 24 kg/h di granuli e 6 Kg/h di polvere per un totale di 30kg/h ed il master prodotto avrà una percentuale di polvere pari al 20% come programmato.
Tuttavia questi dati non sono sicuri finchè si lavora soltanto con le tramogge volumetriche, specialmente per le polveri, per le quali il rate di alimentazione dipende molto da come le polveri fluiscono perché esse hanno tendenza a creare ponte e non fluire liberamente.
Questo non è il solo problema con l’utilizzo di tramogge volumetriche. Supponendo di voler incrementare la portata non si possono incrementare i numeri di giri in proporzione perché la velocità di avanzamento, specialmente per le polveri, non è lineare; quindi per cambiare le percentuali di composizione bisogna fermare la macchina e rifare la calibrazione dal principio.
Il vantaggio nell’utilizzo dei sistemi di alimentazione gravimetrici
La figura mostra il nostro alimentatore gravimetrico che può essere utilizzato sia per alimentare la bocca principale dell’estrusore che un un alimentatore laterale. Ci potrebbe addirittura essere essere un terzo alimentatore gravimetrico che alimenta pigmenti in un alimentatore laterale.
Si possono usare più alimentatori gravimetrici che lavorano su un ‘unica bocca di alimentazione. Idealmente ogni alimentatore gravimetrico per alimentare un componente, per esempio se ne può avere uno per alimentare i granuli ed un secondo per alimentare le polveri nelle dosi volute.

Essi sono conosciuti come alimentatori “loss in weight” perché calcolano quanto materiale viene ‘perso’, cioè viene svuotato dalla tramoggia in un certo tempo. Le tramogge di questi alimentatori possono essere caricate sia in manuale che in automatico tramite una seconda tramoggia posta in capo alla prima ed a questa collegata mediante un condotto munito di valvola.
Questa seconda tramoggia può essere munita di un agitatore comandato da un motore ad ingranaggi, assolutamente necessario quando le polveri non fluiscono liberamente (tipo riempitivi, pigmenti, etc).
La tramoggia dell’alimentatore gravimetrico non deve essere riempita di continuo perché l’operazione disturberebbe il sistema di misura molto sensibile. Viceversa bisogna lasciare che quasi si svuoti prima di riempirlo di nuovo. Le operazioni di riempimento e di arresto riempimento possono essere programmate dal controllore dell’alimentatore gravimetrico.
Il controllore dell’alimentatore gravimetrico è di facile utilizzo e non richiede calibrazioni perché essi lavorano con qualsiasi tipo di materiale ad una velocità di alimentazione prefissata (grammi o altre unità di misura) e si regolano semplicemente impostando una quantità/minuto oppure ora, con un’accuratezza pari a 0,5%.
Per esempio, se si lavora con 20kg/h sull’alimentatore principale e 10 kg/h sulla seconda unità, si ha un totale di 30kg/h. Se si vuole raddoppiare la portata è sufficiente impostare 60kg/h ed il sistema si adeguerà automaticamente mantenendo le proporzioni già impostate.
L’utilizzo dell’alimentatore laterale richiede un maggior rapporto L/D.
La camera di estrusione di un estrusore bivite è di tipo modulare (moduli di lunghezza 4D, dove D è il diametro della vite) e quindi può essere scelta di diverse lunghezze in funzione del processo. L’inserimento di un alimentatore laterale rende inefficace la sezione in cui si inserisce nella camera di estrusione, per cui è consigliabile allungare la camera di estrusione di 4D per ogni alimentatore laterale inserito.
La camera di estrusione che ha mostrato ottime prestazioni in termini di compounding con alte percentuali di fillers, pigmenti e altri additivi e quella lunga 40D. Come si è detto è bene aggiungere un modulo 4D per ogni alimentatore laterale aggiunto.

Utilizzo di più alimentatori laterali
È possibile utilizzare più alimentatori laterali, che possono essere utili se di devono alimentare materiali a bassa densità molto voluminosi, tipo fibre di vetro o di legno. In questo caso non vi è sufficiente volume alla confluenza dell’alimentatore laterale con la camera di estrusione per poter introdurre tutto il materiale di alimentazione quindi si deve dividere l’alimentazione degli additivi tra due alimentatori laterali. Il secondo alimentatore va posizionato ad alcuni moduli di distanza per dare al sistema il tempo necessario ad integrare il materiale proveniente d primo alimentatore, che dovrà passare attraverso una serie di sezioni di kneading per poter essere adeguatamente omogeneizzato prima di affrontare l’introduzione del successivo lotto di fibre. Come già spiegato l’inserimento di 2 alimentatori laterali implica l’allungamento della camera di estrusione a 48L/D e l’utilizzo di 3 tramogge gravimetriche, una posizionata sulla bocca di alimentazione principale ed una per ciascun alimentatore laterale.
Utilizzo di un alimentatore laterale come sistema di degasaggio
Con alcuni materiali tipo fibre di legno ci sono alti contenuti di umidità che non si riesce ad eliminare solo con il dispositivo di degasaggio standard presente nel sistema. Inoltre, quando il materiale ha alti contenuti di umidità si gonfierà in modo sostanzioso fino a bloccare l’aspirazione del dispositivo di degasaggio.
In questi casi si può ovviare al problema collegando sulla camera di estrusione un alimentatore laterale per fare il vuoto. Le viti dell’alimentatore laterale ruotano ad alta velocità per respingere eventuale materiale risalente dalla camera di estrusione principale ed allo stesso tempo permette l’espulsione dell’umidità dal sistema.
